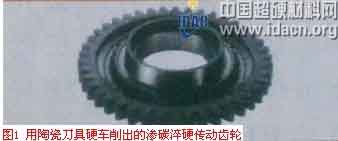
When using ceramic tools to process difficult-to-machine materials such as ordinary steel, cast iron, hardened steel, high manganese steel, nickel-based superalloy, powder metallurgy sintered parts, FRP and various engineering plastics, the tool life can be several times higher than that of cemented carbide tools. More than ten times. In production, it can be used not only for general car, boring and milling, but also for hole machining tools. It can be effectively used in CNC machine tools and machining centers, in addition to ordinary machine tools. On the equipment, it is internationally recognized as one of the most promising tools for improving production efficiency in the contemporary era. In addition, compared with superhard tools such as diamond and cubic boron nitride, the price of ceramic tools is relatively low (the main raw material of ceramic tools, such as alumina and silica, is the most abundant component in the earth's crust, which is inexhaustible.) Inexhaustible), therefore, some people believe: "With the continuous improvement of the performance of modern ceramic tool materials, it will become high-speed cutting, dry cutting and superhard tools such as coated carbide tools, diamond and cubic boron nitride. Three main tools for hard cutting.†Figure 1 shows the synchronous conical section, inner bore and back of a carburized hardened transmission gear (57 HRC∼59 HRC) that is hard-turned with a ceramic cutter instead of being ground. Application examples.
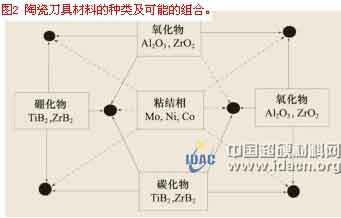
Compared with cemented carbide tools, ceramic tools have a hardness of up to 92∼95 HRA and good wear resistance. When machining steel under the same conditions, its wear is only 1/15 of that of P10 (YT15) carbide tools. long life. At the same time, ceramic knives have low affinity with metal materials such as steel, low friction coefficient, strong anti-adhesion and anti-diffusion ability, and are not easy to stick and produce built-up edge during cutting, and the surface quality is good. The ceramic tool also has good heat resistance and can maintain a high hardness of about 80 HRA at 1,200 ° C, so it is suitable for high-speed cutting and dry cutting at high temperatures, and the price is far lower than the diamond and cube with similar cutting performance. Boron nitride tool. Table 1 shows the comparison of the properties of ceramics and common hard alloys.
As can be seen from Table 1, the main disadvantages of the ceramic cutter are low bending strength, fracture toughness and elastic modulus, and high brittleness. For a long time, it has been mainly used as a finishing tool, accounting for a small proportion of various types of tool materials. However, in the past ten years, due to the advancement of materials science and manufacturing technology, by controlling the purity and grain size of raw materials, hot pressing and hot isostatic pressing sintering processes (ceramics made by hot pressing sintering, strength and Hardness is better than the cold pressing method in the past; ceramics made by hot isostatic pressing have dense structure, higher strength and good chipping resistance, and various carbides, nitrides, borides and oxides are added. It can improve the performance of ceramics and improve its fracture toughness and strength through the synergy of particles, crystal repair, phase transformation, microcracks and several toughening mechanisms, not only increasing the flexural strength of ceramics to 0.9∼1.0 GPa (maximum Up to 1.3∼1.5 GPa, which is equivalent to cemented carbide), and its impact resistance is also greatly improved, the application range is expanding, in addition to general finishing and semi-finishing, it can also be used under impact load. roughing.
Classification of ceramic tool materials
Most of the modern ceramic tool materials are composite ceramics, and their types and possible combinations are shown in Figure 2. At present, the ceramic tool materials widely used at home and abroad and the ceramic tool materials being developed are basically combined according to the method shown in Fig. 2, and different toughening and reinforcing mechanisms are adopted for the microstructure design, in which alumina ( Al2O3) and silicon nitride (Si3N4) based ceramic tool materials are the most widely used.
Alumina (Al2O3) based ceramic tool material
Pure alumina ceramic
Al2O3 in pure alumina ceramics accounts for more than 99.9%, mostly white, commonly known as white ceramics. This is an early-use ceramic. Due to its low strength, low thermal shock resistance and fracture toughness, it is easy to chip when cutting. It is only suitable for continuous surface roughing and semi-finishing of cast iron and steel below 300HBW. Limited, it has been replaced by various other Al2O3-based composite ceramics.
Alumina-carbide composite ceramic
It is a ceramic which is hot-pressed and sintered by adding TiC or SiC to the Al2O3 matrix. It is one of the most widely used ceramic tool materials at home and abroad. Alumina-carbide composite ceramics are suitable for processing various steel materials (carbon structural steel, alloy structural steel, high strength steel, high manganese steel, bearing steel, stainless steel, hardened steel, etc.) and various cast irons (including chills). Cast iron, high chromium cast iron, etc.), can also process copper alloy, graphite, engineering plastics and composite materials; processed steel is better than Si3N4 based ceramic tool; but it is not suitable for processing aluminum alloy, titanium alloy and tantalum alloy, otherwise it is easy to produce chemistry Wear and tear.
Nano cermet cutter
It is a new type of Al2O3 based ceramic tool modified by adding nano materials TiN (titanium nitride) and AlN (aluminum nitride) in traditional Al2O3 / TiC cermet, which can refine grains and optimize Mechanical properties of the material. The use shows that this is a new type of tool with high technology content and high added value. It can partially replace the K20 (YG8), P10 (YT15) and other large-scale carbide tools, the tool life can be increased by more than 2 times, and the production cost is Equal or slightly lower than the K20 (YG8) tool. At present, nano-ceramics and nano-composite ceramic tools have become a frontier field in the research and development of high-tech ceramic materials.
Al2O3 / SiCw whisker toughened ceramic
20% ∼30% SiCw whisker (a single crystal with a diameter of less than 0.6μm and a length of 10∼80μm) having a certain fiber structure, a tensile strength of 7 GPa and a tensile modulus of over 700 in the Al2O3 ceramic matrix. GPa) Al2O3 / SiCw whisker toughened ceramics can be effectively used in interrupted cutting and roughing, milling and reaming processes, suitable for processing nickel-based alloys, high-hardness cast iron and hardened steel. SiCw whiskers act like steel bars in reinforced concrete, which can become obstacles to block or change the development of cracks, and greatly improve their toughness.
Al2O3 / (W, Ti) C gradient functional ceramics
It compensates for the external load stress during cutting by controlling the composition distribution of the ceramic material to form a reasonable gradient, which produces a favorable residual stress distribution inside the tool. It has the characteristics of high surface thermal conductivity, favorable heat transfer, low thermal expansion coefficient, good structural integrity and easy to break. The tool life when processing steel materials can be 1.5∼1 times higher than that of the similar Al2O3/(W, Ti)C composite ceramic SG-4, and the knife has good self-tanning property, and can still perform normal cutting after chipping.
Composite ceramics such as Al2O3 / TiB2 and Al2O3 / ZrO2
The addition of TiB2, Ti(C,N), ZrO2 and other ceramics to Al2O3 can further improve the physical and mechanical properties and cutting performance of the material, among which Al2O3/TiB2 and Al2O3/ZrO2 are used more. When machining 40CrNiMoA steel with Al2O3/TiB2 ceramic tool, the tool life is 3 times that of Al2O3/TiC tool. When machining 4Cr5MoVSi steel, the tool wear resistance is 2 times that of Al2O3 / TiC tool. The Al2O3 / ZrO2 ceramic tool material has high fracture toughness, strength and wear resistance, and good anti-cracking performance. For example, CC620 blade roughing and semi-finishing iron and ductile iron can be used for cutting speeds up to 900 m/min. When machining alloy steel, the cutting speed of roughing can reach 200 m/min. 800 m/min.
Silicon nitride (Si3 N4) based ceramic tool material
Si3N4 ceramic is a non-oxide engineering ceramic with a hardness of 1,800 ∼ 2,000 HV, good thermal hardness, can withstand high temperatures of 1,300 ∼ 1,400 ° C, less chemical reaction with carbon and metal elements, and lower friction coefficient. These tools are suitable for cutting cast iron, superalloys and nickel-based alloys, especially for high feed or interrupted cutting. Since pure Si3N4 ceramic tools are prone to crater wear when cutting long chips (such as mild steel), the new Si3N4 ceramics are Si3N4 composite ceramic tools. The latest Si3N4 composite ceramics can be used not only for roughing, but also for interrupted cutting and coolant cutting. At present, the chipping rate of Si3N4-based ceramic tools is 2% ∼ 3%, which is equivalent to cemented carbide and can be applied to a large number of production lines. The disadvantage of this type of ceramic tool is that the workability is worse than that of ordinary Al2O3 ceramics.
Si3 N4 / TiC composite ceramic
Its toughness and flexural strength are higher than that of Al2O3-based ceramics, but the hardness is not reduced; the thermal conductivity is also higher than that of Al2O3-based ceramics, so it is widely used in production.
Si3 N4 / SiCw whisker toughened ceramic
It is made by adding a certain amount of carbide whiskers to the Si3N4 matrix, thereby improving the fracture toughness of the ceramic tool. The grades produced in China are SW21 (Si3N4/ SiCw) and FD03 (Si3N4/TiCw). Some foreign cutting experts believe that the effect of cutting steel with Si3N4 based ceramics is not as good as that of Al2O3 based composite ceramics, so it is not recommended to process steel. However, it also has good effects when cutting hardened steel (60∼68HRC), high manganese steel, high chromium steel and bearing steel with FD03 blade.
Sialon Ceramics
It is made of Si3N4 as hard phase, Al2O3 is wear-resistant phase, and a small amount of sintering aid Y2O3 is added and sintered by hot pressing, often called Sialon. Sialon is a general term for a large class of solid solutions in which Si and N atoms are replaced by Al and O atoms in Si3N4. There are three kinds of β-Sialon, α-Sialon and O-Sialon, especially the two. The ceramic has high flexural strength and fracture toughness, good oxidation resistance and high temperature creep resistance, high thermal conductivity, small thermal expansion coefficient and good thermal shock resistance, suitable for roughing and milling of cast iron and nickel base. Difficult to machine materials such as superalloys. In addition to high-speed machining of cast iron and high-temperature alloys with large feed rates and cutting speeds, double positive rake angles (positive values ​​for both the front rake angle and the front rake angle) can be used on the face milling cutter.
Coated Si3N4 ceramic tool
The toughness of Si3N4-based ceramics is better than that of Al2O3-based ceramics, but its wear resistance is slightly poor. When cutting cast iron, the flank wear of Si3N4 ceramic tool is greater than that of Al2O3 ceramic tool; when cutting steel material, the crater wear of Si3N4 ceramic tool is larger. To this end, foreign countries apply SiN, TiC, Ti (C, N) and Al2O3 coatings on the surface of Si3N4 based ceramics, which can be single-coated or multi-coated. The coated Si3N4 ceramic tool wears 1/3 of the uncoated layer, which makes the cutting speed of ordinary cast iron reach 200∼1,000 m/min and the tool life is longer. For example, Sandvik's GC1690 coated silicon nitride ceramic tool has a feed rate of 0.4 mm/r and a cutting speed of 500 m/min when machining high-strength gray cast iron. Seco's coated silicon nitride ceramic tool has strong ability to resist crater wear when cutting steel. Its cutting speed can reach the cutting speed of Al2O3 based ceramic tool, but the feed rate is larger than the latter and close to coating. The layer of carbide cutting tool greatly improves the material removal rate.
How to choose ceramic tool materials
At present, Al2O3-based ceramics and Si3N4-based ceramics have been successfully used to make cutting parts for turning tools, boring tools and milling cutters. The structure of ceramic cutters is currently mostly in the form of a structure of a machine-foldable indexable insert. The shape of the blade is triangular, square, rectangular, prismatic, and circular.
There are dozens of varieties of ceramic blade materials. Different types of ceramic blades have different application ranges. Therefore, the types and grades of tool ceramics must be correctly selected to match the materials to be processed. In addition to meeting technical requirements, economic and environmental performance requirements should also be met.
Alumina (Al2O3)-based ceramics have good wear resistance and heat resistance, and their high-temperature chemical stability is not easy to interdif or chemically react with iron, and their wear resistance and heat resistance are higher than Silicon nitride (Si3N4) based ceramic tools, so Al2O3 based ceramic tools have the widest application range, suitable for high speed machining of steel, cast iron and their alloys; processed steel is superior to Si3N4 based ceramic tools; but it is not suitable for processing Aluminum alloys, titanium alloys and niobium alloys, otherwise chemical wear is likely to occur.
Silicon nitride (Si3N4) based ceramic tool with high fracture toughness and thermal shock resistance. Al2O3 based ceramic tool is most suitable for intermittent processing of cast iron and high temperature alloys. It is generally not suitable for processing steel with long chips (such as normalizing). And hot rolled state), the tool wear when cutting 45 steel with Si3N4 based ceramic tool is much higher than when cutting gray cast iron.
Sialon ceramics are best suited for processing a variety of cast irons (such as gray cast iron, ductile iron, chilled cast iron, high alloy wear resistant cast iron, etc.) and heat resistant alloys, and are generally not recommended for processing steel.
Inconel 718 (GH169) nickel-based alloy is a typical hard-to-machine material with high high-temperature strength, dynamic shear strength, small thermal diffusivity, and work hardening during cutting, resulting in high tool cutting temperature and accelerated wear rate. Al2O3 / SiCw whisker toughened ceramics are suitable for processing nickel-based alloys with low hardness. Longer tool life is achieved at cutting speeds of 100∼300 m/min; an IW7 whisker toughened ceramic produced by ISCAR The new grade of Al2O3 / SiCw), from the processing of high-temperature alloy turbine discs such as Inconel 718 and nickel-based heat-resistant alloys, shows a significant improvement in cutting performance and tool life compared to other ceramic inserts. Si3N4-based ceramics can also be used in the processing of Inconel 718 alloys. Sialon ceramics have high toughness and are suitable for cutting solution-treated Inconel 718 (45HRC) alloys.
In addition, Kevlar and graphite composites for aerospace use ceramic tools for high-speed machining at cutting speeds of around 300 m/min.
It must be pointed out that ceramic inserts are not classified internationally like cemented carbide. Each production plant has its own varieties and grades. The performance of similar blades produced by different factories also has certain differences. When using, you must refer to the manufacturer's product samples. Come choose. For this reason, after the blade grade is selected, it must be tested on the machine tool first, and then it can be formally applied after passing the test.
Ceramic tool application recommendations
Ceramic knives have changed the traditional machining process and solved many of the previously difficult machining problems in production. It is widely used in machinery, metallurgy, mining, high-speed trains, wind power, automobiles, tractors, bearings, pumps, transportation, energy, precision instruments, aerospace and other industries and has achieved significant economic benefits.
China has an advantage in the research and development of ceramic knives, which was used in production as early as the 1950s. For example, China's ceramic and cemented carbide composite blades (FH series), the surface of the workpiece has both high hardness and wear resistance of the ceramic material, while the base has a good bending strength of the hard alloy, and its equivalent bending resistance. The strength is 20% higher than the average ceramic blade, the fracture toughness is increased by 8.5% on average, and its resistance to breakage is increased. Therefore, it can withstand the impact load and solve the problem of difficulty in inserting and welding ceramic blades. In addition, new varieties of tool ceramics developed at home and abroad in recent years, such as ZrO2-based ceramics and TiB2-based ceramics (hardness is twice that of silicon nitride), which are suitable for processing various aluminum alloys (including aluminum alloys with high silicon content). The performance is between cemented carbide and superhard CBN, and the tool life when machining hardened steel and high temperature alloy is 5-6 times longer than that of cemented carbide tools, although their production has not yet formed scale. However, due to its excellent performance and wide range of uses, it will develop rapidly in the future.
Machine tools using ceramic tools must have high stiffness, high power, high speed and high precision, so that the performance of ceramic tool materials can be fully utilized and good economic benefits can be achieved. In addition, the fixture and clamping device for clamping the workpiece must be highly reliable to avoid vibration during machining and damage the tool. It must be pointed out that many of the current machine tools in production cannot meet the processing requirements of ceramic tools, so their potential has not been fully utilized. In the future, with the increase in the use of high-efficiency equipment such as CNC machine tools and machining centers, it will be further promoted. The use of ceramic tools.
Due to the high brittleness and low strength of the ceramic tool material, the rake angle of the tool is usually 0°∼-10°, and the back angle is 5°∼12°. In order to improve the strength of the cutting edge, the chamfer must be ground with a negative chamfer. The width of the chamfer can be b = 0.1 ∼ 0.8 mm, the chamfering angle is -10 ° ∼ -20 °; the tip of the blade needs to be properly rounded, and the radius of the rounding is r = 0.2 ∼ 1.0mm. However, the larger the radius of the tool nose and the negative chamfer, the greater the cutting force and the greater the chance of chattering. Therefore, when the system rigidity of the machine tool-clamp-tool-workpiece is insufficient, especially when machining an elongated workpiece, it is not appropriate to use an excessive tool nose radius and negative chamfering.
Since ceramic knives have good heat resistance and wear resistance, the amount of cutting affects tool wear less than that of cemented carbide tools. Therefore, according to the material properties of the workpiece to be machined, under the premise of the machine power, the rigidity of the process system and the strength of the blade, try to use a larger amount of backing knife (deep depth) and cutting speed to make full use of the ceramic tool. The material has good high temperature performance. While some companies use ceramic tools, they believe that lower cutting speeds can extend tool life. Cutting speed, turning ordinary steel and cast iron, generally Vc=200∼600 m/min; high hardness steel with processing hardness of 65HRC Vc=60∼200 m/min; milling steel and cast iron Vc=200∼500 m/min; milling Heat resistant alloy Vc=100∼250 m/min, feed rate 0.05∼0.08 mm/z.
The sharpening of the ceramic knives should be sharpened with a jig on the tool grinder to ensure the quality of the sharpening. Grinding ceramic tools are mostly made of resin bonded diamond wheels, and the grinding quality has a great influence on the cutting performance of the tool. In principle, the indexable ceramic inserts are not regrind, because the clamping size and positioning size of the inserts will change after regrind. In the CNC machining, the infeed size must be re-adjusted to ensure the workpiece size. consistency. However, some factories use the diamond grinding wheel to sharpen the tool grinding machine or the tool sharpening machine in order to reduce the consumption. The grinding machine uses F80∼F120 grain size, fine grinding and fine grinding with F180∼F400 grain number. The concentration is 50% ∼ 100%, and the hardness is K ∼ P level. The cutting amount during sharpening can be as follows: grinding speed 20∼30m/s, grinding depth f=0.005∼0.02 mm/double stroke (large value in rough grinding, small value in fine grinding and fine grinding), workbench The speed is V = 10 ∼ 15 m / min.
Hdpe Anti-Root Membrane Use high strength polyethylene after extrusion, smooth surface with high corrosion and weather resistance, waterproof effect is good, thorn resistance significantly. Suitable for planting roof, Roof garden, the garage roof greening and need the underground building roof engineering.
1) Has excellent waterproof function, can form high strength waterproof layer, the ability to resist water pressure is strong, maintain the long-term effects of water;
2) Has prevented the plant root penetration function, can withstand the plant root system puncture. Preventing root, but also does not affect the normal growth of plants;
3) The product of high tensile strength, corrosion resistance, mold resistance, good weatherability;
4) Excellent high and low temperature performance of base contraction deformation and cracking of the strong ability to adapt, suitable for hot and cold region can be.
Spec Properties |
GM1.0 |
GM1.25 |
GM1.5 |
GM2.0 |
GM2.5 |
Thickness |
1.00mm |
1.25mm |
1.50mm |
2.00mm |
2.50mm |
Density ( ≥) |
0.940g/cc |
0.940g/cc |
0.940g/cc |
0.940g/cc |
0.940g/cc |
Tensile Properties ( ≥) • yield strength • break strength • yield elongation • break elongation |
13 kN/m 20 kN/m 11% 600% |
16 kN/m 25 kN/m 11% 600% |
20 kN/m 30 kN/m 11% 600% |
26 kN/m 40 kN/m 11% 600% |
33kN/m 50kN/m 11% 600% |
Tear Resistance ( ≥) |
115 N |
140 N |
170 N |
225 N |
280 N |
Puncture Resistance ( ≥) |
240 N |
300 N |
360 N |
480 N |
600 N |
Carbon Black Content ( ≥) |
2.0-3.0% |
2.0-3.0% |
2.0-3.0% |
2.0-3.0% |
2.0-3.0% |
Carbon Black Dispersion ( ≥) |
Note(1) |
Note(1) |
Note(1) |
Note(1) |
Note(1) |
Oxidative Induction Time(OIT) Standard OIT ( ≥) |
60 min. |
60 min. |
60 min. |
60 min. |
60 min |
Hdpe Anti-Root Membrane,Hdpe Dimple Membrane,Plastic Sheet Membrane,Waterproofing Membrane
Shandong Tianhai New Materials Engineering Co., Ltd , http://www.chinatinhy.com